How Do You Ensure Quality Control as Your Business Scales?
To help small business owners maintain quality control as their business scales, we asked various leaders this question for their best strategies. From balancing quality checks and efficiency to adopting a tiered quality-check system, here are eight insights shared by operations managers and company presidents on effective quality control processes.
- Balance Quality Checks and Efficiency
- Embed Quality Standards in Company Culture
- Standardize Procedures for Consistent Quality
- Foster Pride in Quality Work
- Combine Training with Quality Checks
- Build a Robust User Feedback Loop
- Implement Checks and Balances System
- Adopt a Tiered Quality-Check System
Balance Quality Checks and Efficiency
I've had a variety of different roles in various industries. One of my favorites was the five years I spent as a Quality Assurance Manager in manufacturing consumer-packaged goods, so quality control is near to my heart.
Quality checks ultimately come down to a balance between the risk of error or sub-par work versus the time it takes to check. If you don't put enough checks in, you are letting unacceptable work pass through at a high rate. If you put too many checks in place, you are wasting a lot of man-hours doing checks that do not provide value, and this can be frustrating for your employees on top of being financially costly.
How do you strike the balance? Start by building systems and iterating on them.
As an entrepreneur with a new business, you start with nothing and have to build it from scratch, so in the beginning, you are most likely moving forward with no systems and just getting things done. Start by writing out your processes, nothing fancy, just get it down on paper.
After that, you test your processes and adjust them as needed. Your processes might already have built-in quality checks that you recognize as necessary, or maybe they don't yet because you don't see the need for checks with your small killer team that doesn't make mistakes.
Finally, you address and assess quality problems as they arise. Each error, sub-par performance, and customer complaint is an opportunity to improve your processes. You don't have to change your process every time there is an issue, nor should you, but you should be assessing each issue and asking yourself if there is anything you can improve as a result of this new information.
For example, how would I approach a situation where one of our electricians installed the incorrect light fixture in a room? First, I'd need to determine the root cause. Were the written instructions incorrect or unclear? Did someone on the job site give conflicting instructions? Or was everything clear, but our employee simply wasn't paying attention? If it's the latter, it might require some corrective action with that individual. However, if the instructions were unclear or conflicting, we might need to add a quality check at the beginning of projects – for instance, walking through each project with the client and ensuring all our documentation matches their exact requests.
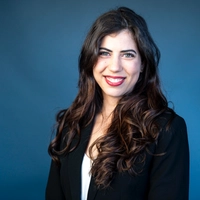
Embed Quality Standards in Company Culture
A key principle I have followed is to establish clear quality standards early on and embed them into the company culture. A strategy I have found is to implement a robust quality-control process that involves defining specific quality metrics, setting clear expectations, and establishing regular checkpoints. This includes unit testing, integration testing, and user acceptance testing.
Beyond the product or service, it's equally important to maintain quality in customer service and support. We use customer satisfaction surveys and net promoter scores to measure performance, as well as implement a customer feedback loop to identify areas for improvement and address issues promptly. We have found regular training for customer service representatives is also important to provide consistency in handling customer inquiries and complaints.
To maintain quality as the company grows, it's crucial to empower employees at all levels to take ownership of quality. This can be achieved through training programs that emphasize the importance of quality and provide employees with the tools and knowledge to identify and resolve quality issues. Creating a culture of continuous improvement encourages our employees to suggest and implement enhancements to processes and products.
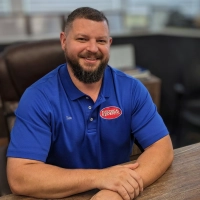
Standardize Procedures for Consistent Quality
Ensuring quality control as a small business scales is a challenge I've faced firsthand. One effective approach is implementing standardized procedures across all operations. When I started scaling SEO-Optimizers, I realized that having clear, documented processes for each task was crucial. This consistency ensured every team member knew exactly what was expected, reducing errors and maintaining quality.
For example, we developed a comprehensive checklist for our SEO audits. Each audit must pass through multiple layers of review before being finalized. Initially, a junior analyst conducts the audit using our detailed checklist, which includes steps like keyword analysis, site-structure evaluation, and content review. This audit is then reviewed by a senior analyst who verifies the findings and makes necessary adjustments. Finally, I conduct a final review to ensure nothing is missed and that the audit aligns with our standards. This layered approach not only maintains quality but also provides training opportunities, ensuring our team continually improves.
By embedding quality checks into our workflow and fostering a culture of accountability, we can scale our business without compromising the high standards our clients expect.
Foster Pride in Quality Work
As a manufacturer of rustic-luxury handrails for use in new construction and remodels, shipping nationwide, quality control is of the utmost importance to us. The best way that I have found is to make sure that everyone on the team has a high level of pride about the quality of their work. We do this by finding people that fit the company culture of producing the highest level of quality. Throughout the process, we need to ask ourselves, "Is this something I would be proud to have on display in my own personal home?" And the answer to this needs to consistently be a resounding "Yes!"
Combine Training with Quality Checks
Maintaining consistent quality is so important in the HVAC industry. As our company has grown, we've implemented several strategies to uphold our service standards. One component is a rigorous technician-certification program. All of our technicians undergo comprehensive training on the latest equipment, industry best practices, and customer service. This ensures that every customer receives top-notch service, regardless of the technician assigned to the job.
To complement our training initiatives, we've established a quality-check process. After every service call, customers complete a satisfaction survey. We meticulously analyze these surveys to identify areas for improvement. Additionally, we conduct random quality checks on completed jobs, ensuring that work adheres to our standards. For instance, we might inspect equipment installation photos, review customer feedback, and verify compliance with safety regulations. By combining technician training with a comprehensive quality-check process, we've been able to maintain our reputation for excellence while scaling our operations.
Build a Robust User Feedback Loop
I’ve had firsthand experience ensuring quality control as our business scales. One of the key strategies we implemented was building a robust feedback loop with our users. Early on, we realized that maintaining high-quality standards requires continuous input from those who use our platform daily. To facilitate this, we created a dedicated user-feedback team that gathers insights and suggestions directly from our customers. This feedback is systematically analyzed and used to inform product updates and feature enhancements, ensuring that our services meet the evolving needs of our users.
A specific example of our quality-check process involves our automated social media posting feature. To ensure it performs flawlessly, we implemented a multi-layered testing protocol. This process includes automated unit tests that check the functionality of individual components, integration tests that ensure different parts of the system work together seamlessly, and user acceptance tests where real users test the feature in a controlled environment. This rigorous approach has helped us identify and resolve issues before they affect our broader user base, maintaining the high-quality standards our customers expect from RecurPost.

Implement Checks and Balances System
One effective strategy I've implemented is creating a robust system of checks and balances throughout our processes. By taking an approach similar to NASA's, we double-check everything and establish multiple filters within our workflows to catch any potential mistakes. For example, in our client intake and case management system, we have developed a detailed checklist that must be followed for every new client. This checklist includes verifying client information, ensuring all necessary documentation is collected, and conducting a thorough initial consultation to understand the client's needs and circumstances.
We have also implemented a peer-review system where cases are periodically reviewed by senior staff members. This means that once a legal document is prepared, it goes through multiple layers of review—first by the assigned attorney, then by a senior associate, and finally by me. This multi-tiered review process helps catch any potential errors or oversights, ensuring that our clients receive the highest quality legal service.
By creating these checks and balances, doubling down on everything, and establishing multiple filters in our processes, we can catch mistakes and maintain high-quality service as our business grows. This approach not only ensures consistency and excellence in our work but also helps build trust and satisfaction among our clients.
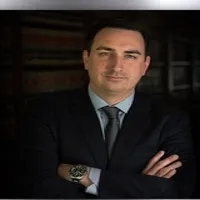
Adopt a Tiered Quality-Check System
Scaling up a business like Sartoro requires a keen eye on quality control to ensure we don’t lose what made us great in the first place. One effective approach we’ve adopted is implementing a tiered quality-check system. At our production facility, we start with a detailed inspection during the assembly process, focusing on stitching, fit, and fabric integrity. Afterward, our quality team conducts a final review before shipment, checking for consistency and overall craftsmanship.
For instance, when we expanded our production line last year, we introduced a “checkpoint review” where every suit is randomly selected from the batch for an additional quality audit. This helped us catch a few minor issues early, ensuring every garment met our high standards. Balancing growth with quality can be a tightrope walk, but these processes help maintain the excellence our customers expect while scaling effectively.
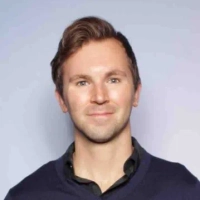